
I have an 8 inch Boxford, but never managed to get around to changing the drive belt. If you look on Google Earth street view at the Nettleham Engineering address, you will find they seem to have diversified into the shopping centre business! Their web site home page was last updated in 2000! I think they may well have ceased trading, at least at the Marshall Yard. To the OP, yes a table support is top priority on that Alba - will transform rigidity and DOC and finish. I try and use butt welded HSS with 5/8" shanks thinned down to fit the tool holder. 100 thou DOC is no problem in even the toughest of steels.

Slightly off-topic, but Nettlehams seem to be very much alive and kicking: They always had quite a few Boxford models in stock. I remember the rows of used, and seemingly unwanted, shapers. Shame they and the buildings are all long gone now. I still have an Elliot pillar drill and Smart & Brown lathe supplied by them.
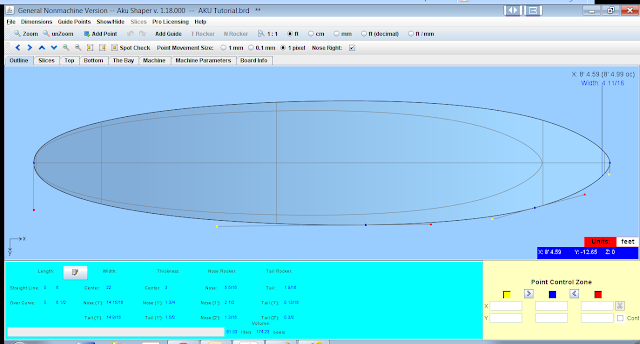
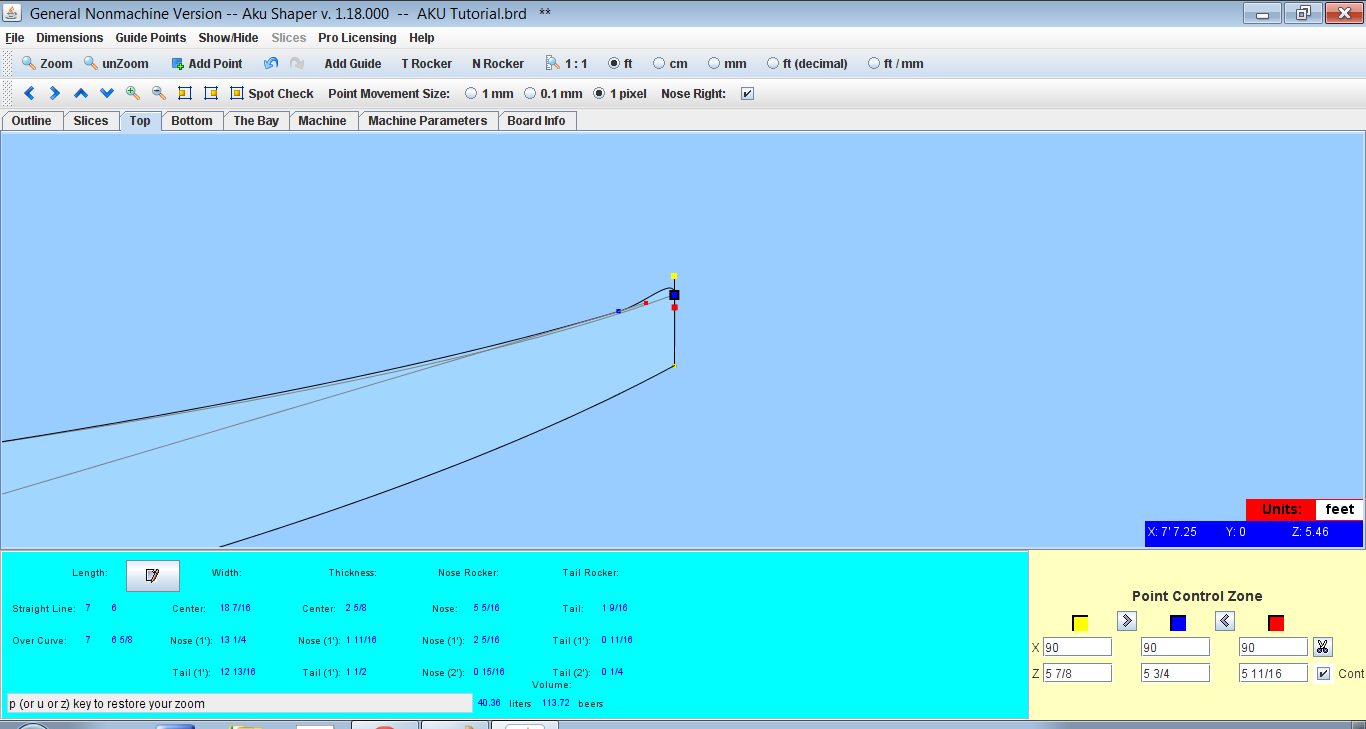
Every couple of months I would pop in to browse through their stock of used machinery, spread throughout the huge building. Years ago I used to visit Nettleham Engineering in Gainsborough, they were a machine tool dealer at the old large Marshall works. It would be handy to know the measurements of the original chip tray fitted to these early type Alba machines. Regarding the lack of a table support, I plan to build one in when I get round to fabricating a heavy steel chip tray. The only thing this model lacked was the table support, which isn't a problem if depth of cut is reasonable. My Alba shaper had both horizontal and vertical feeds, I believe the vertical feed was an optional extra. Yep you'll get a nice surface finish with the shaper and watching the old girl go is very theraputic Now you've mentioned it, I might as well use the shaper to hog it out of a lump of steel rather than use the milling machine. What a great idea, I have often thought about making a solid toolpost to replace the topslide, particularly for large boring bars. Like it, my Boxford is taking down a 3"×3"× 2" Mild steel to make a rigid toolpost for the lathe to replace the compound, played around with depth of cut eventually tried 100 thou went fine until the scotch yoke bit that sets the stroke slipped, I hadn't tightened it up properly I think I'll stick to 10 -20 thou cuts,it ain't a race is it, good luck with yours So another future job will be to make another drive ratchet assembly and a pair of gears to mesh them together. The factory illustration shows two ratchet mechanisms geared together drawn in, but I have not seen any with two ratchets fitted. It has a facility for auto rise and fall of the table, but the single ratchet mechanism has to be swaped over from the cross feed shaft. I had never used a shaper before, and found this machine to be a delight to use. It is located at my place of work, alongside the Burrell Showmans Engine who's flywheel can be seen in the background.Īfter machining a couple of test pieces it was soon put to work machining a new key for the Burrells steering worm wheel.
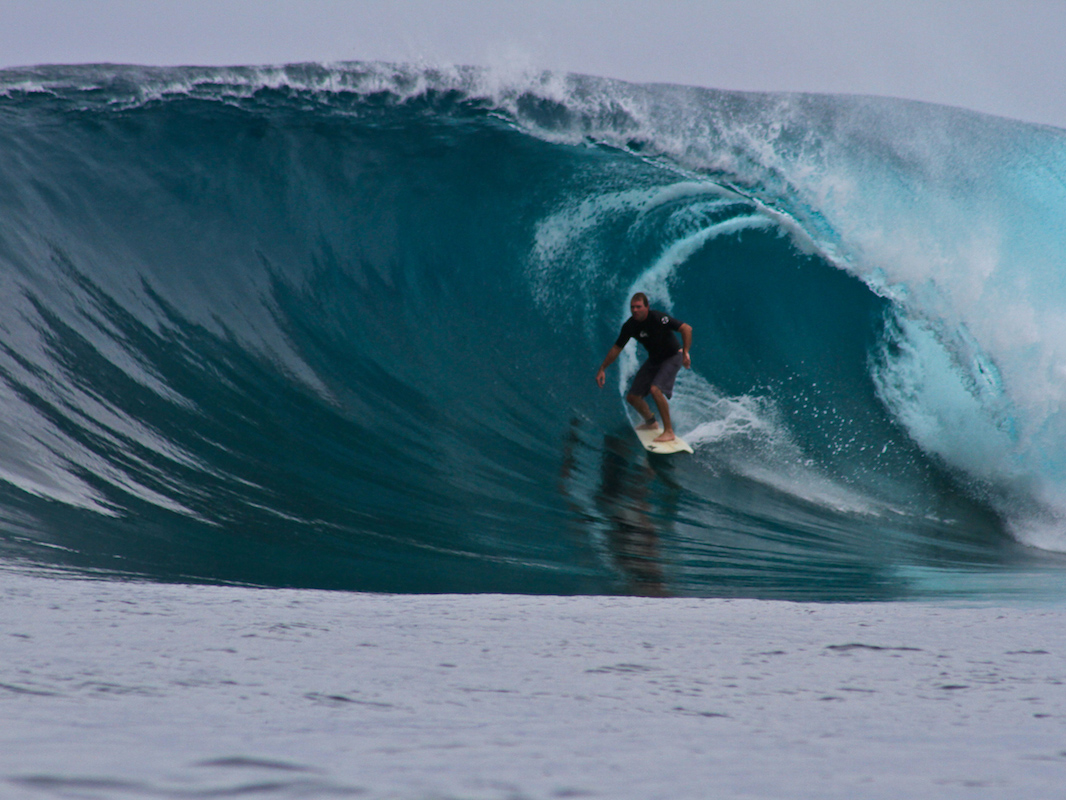
For now it has just had stuck parts freed off, some of the surface rust removed and a good oil up. The cast iron chip tray that sits between the upper and lower main castings is missing, so a new steel one will be fabricated at some point. The rather dodgy position of the motor and the unguarded drive belts will need altering. A couple of months ago I was given this Alba shaper, it would have been rude to refuse it.
